With an annual market penetration rate of 13.4% since 2021, new energy cars have entered a market-driven stage.The industry of charging stations has prospered in large part due to the new energy vehicle market's quick growth. According to the official data provided by China Charging Union, there were 2,253,000 units of charging infrastructure across the country as of the end of October 2021, an increase of 50.4% from the previous year. Among them, there were 1,911,000 private charging heaps, an increase of 43.3% year over year, and 1,062,000 public charging piles, an increase of 59.4%.
The continuous operation of new energy charging equipment necessitates high current, which calls for high stability of the charging equipment in terms of continuous high current. The standard plugs that are used with the charging apparatus must also operate continuously at full load and, in most cases, must be charged continuously for at least 10 hours. This is substantially stricter than the conditions under which typical household appliances are used and the size of the plugs that may transport current, which are not used at full load and are not operated constantly at high current for extended periods of time. Today, we'll look at the 16 A standard plug's overheating issue that occurs when the portable ev charger is used.
This is a portable ev charger device that our business invented and created. It can be connected into any available 16 A power outlet at any time to charge an electric car. charging specifications: 16 A at 220 VAC. For continued full load functioning, it is necessary. Customers complained that once the product was put on the market, the plug temperature was frequently quite high, leading to overheating protection or even overheating and deforming of the plug, burning, and other faults. For the purpose of systematic investigation and improvement verification for this plug over-temperature problem.
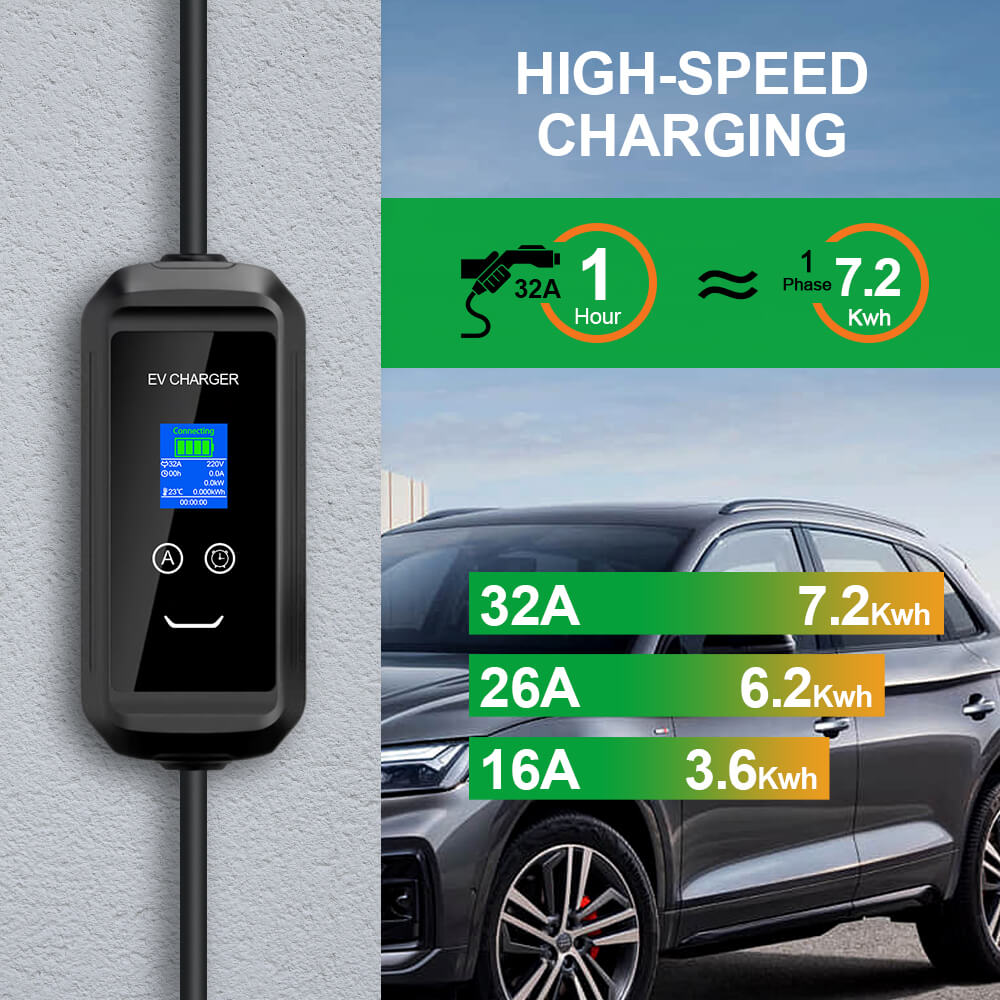
The theory behind the rise in temperature caused by electric current is known as the thermal effect: when an electric current travel through a conductor, heat is produced because of the conductor's resistance. Theoretically, this thermal effect of electric current is explained by Joule's - Corrugated Law, which states that the heat generated by the conductor's resistance as a result of the current passing through it is directly proportional to the square of the size of the current passing through it, the conductor's resistance itself, and the time of the current passing through it.
The contact resistance R2 between the conductors consists of the following two main components:
(1) Concentration resistance: When the current flows through the real contact surface, the resistance is visible as a result of the current line's contraction (or concentration).
(2) Film resistance: This is a result of the film on the contact surface and additional impurities that make up the film resistance. The contact material, positive pressure, surface condition, application of voltage and current, and other factors have a major impact on the size of the contact resistance. It is discovered that as positive pressure rises, concentration resistance falls, contact resistance follows, and as contact area shrinks, contact resistance rises. In other words, the relationship between the contact resistance R2 and the contact pressure F and area S between the conductors is inverse.
According to a review of real charging gun usage, the following two factors may be mostly to blame for the plug on the charging gun overheating during use:

The plug socket overheats for two reasons: 1) The wall socket with which the plug is used is not reasonably designed, causing the plug and socket sleeve contact to be poor (contact resistance to increase) or the conductivity of the socket sleeve (the conductor's internal resistance to be insufficient).
2) The power-supplying plug on the charging gun itself is overheated. The charging gun's power supply plug has an excessively high conductor resistance, which raises the plug's internal temperature when it is completely loaded.
According to the reasons analyzed above, the following test verification:
1) verify the temperature rise of the guest socket: with a qualified plug, with the guest socket temperature rise test; verification data in Figure 3, according to the test data analysis can be found, the guest socket temperature rise data to meet the standard (45 K) requirements, there is no phenomenon of abnormally high temperatures, which led to the conclusion that: the guest back to the outlet to meet the requirements of temperature;
2) verification of the guest plug temperature rise verify the temperature rise of the guest plug: a qualified socket, with the guest plug for temperature rise test; verification data in Figure 4, according to the test data analysis can be found, there are three samples of the guest plug temperature rise data exceeds the standard, the largest temperature rise reached 74.5 K, which concludes that: some of the guest plug over-temperature bad.
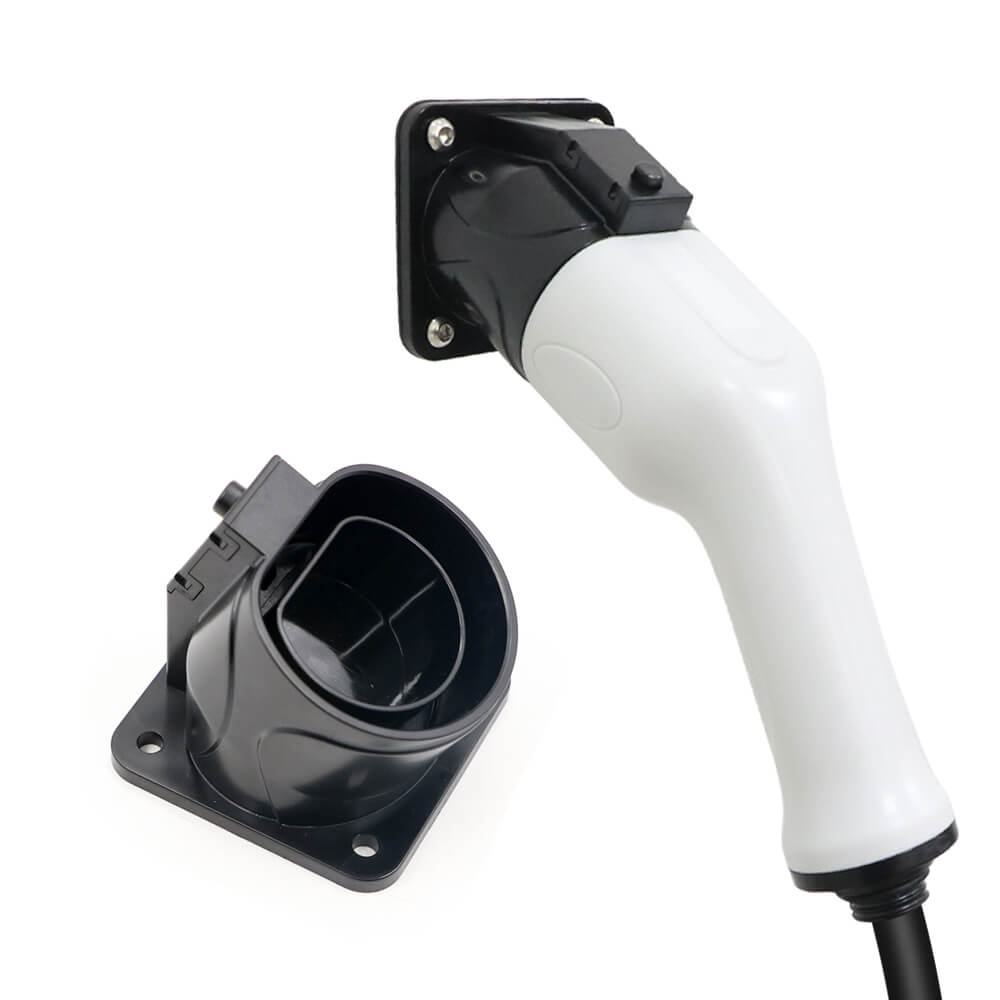
Considering the structure of the bracket and the direction of the riveting process, the common U-shape opening terminal could not meet the requirements, and it would lead to loose wire and torsion riveting defects. We redesigned the riveting structure and chose the hollow cylindrical terminal structure. This structure has two characteristics:
1) To prevent the torsion issue after riveting, this riveting structure is a concentric ring structure, with the concentric ring riveting axis and pin co-axial.
2) To prevent the torsion issue after riveting, it is a closed-loop structure with the riveting axis and the pin co-axial. The mouth is designed with a guided flare construction, which allows the wire harness enough guidance to prevent the problem of bending and breaking of the wire harness. At the same time, it is also a closed ring structure, preventing the problem of loose threads during riveting.
The novel riveting structure has been demonstrated to be able to regulate the needs for riveting firmness and pressure. The temperature increase was then confirmed. The new system clearly improves things, as shown by the analysis of the test data. 5 samples of the L-N pole had the largest temperature rise of 25.7 K, which is far lower than the required 45 K and much lower than the plug's deformation temperature of roughly 110 °C.
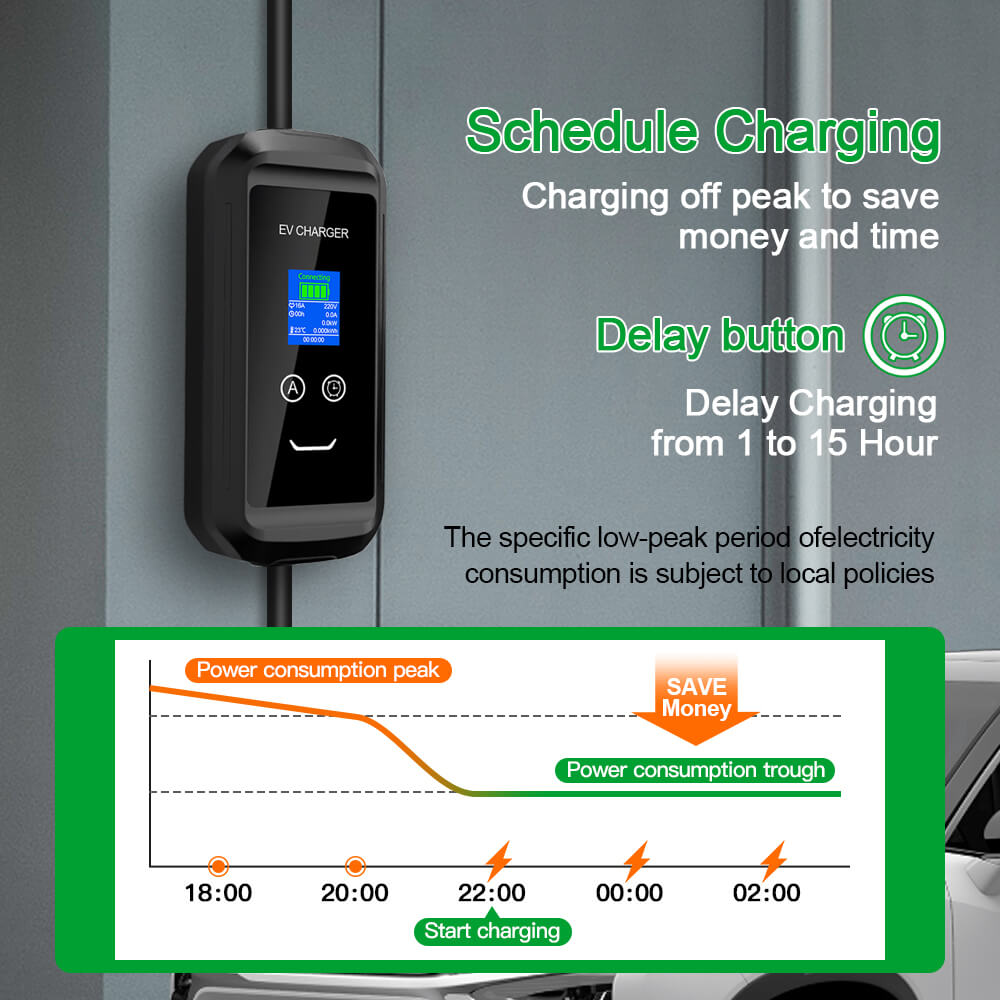
In order to improve our portable ev charger performance .We have developed the process requirements and warnings for riveting wire harnesses as a result of this investigation.A unique and significant process technology is the riveting of wire harnesses. The strength and conductivity of the connection between the harness and the terminals are closely correlated with the quality of the riveting process. We can focus on managing the conductivity of the riveted during the subsequent control process in addition to controlling the pull-off force of the riveted terminal. This study demonstrates the need of taking into account the wire harness terminal structure design when making structural decisions about the terminal and the orientation of the riveting process.